Path to Becoming a Leader in X-ray Innovations with Lennart Schulenburg of VisiConsult
Episode Overview
Episode Topic: In this episode of Skeleton Crew – The Rad Tech Show, we engage with Lennart Schulenburg, a specialist in industrial X-ray safety from VisiConsult, to discuss the non-traditional uses of X-ray technology outside the medical field. We delve into how X-rays play a pivotal role in industries by ensuring the integrity and safety of various non-living objects, highlighting the innovative approaches and technology developments that set industrial applications apart from medical radiology.
Lessons You’ll Learn: This episode provides an in-depth exploration of industrial X-ray safety, offering valuable insights into the sophisticated technology and methods employed to protect users and the environment. Listeners will learn about the stringent safety protocols that companies like VisiConsult implement to mitigate risks associated with high-energy X-rays. Furthermore, the discussion sheds light on the role of artificial intelligence in enhancing the precision and effectiveness of industrial X-ray safety measures, illustrating how cutting-edge technology is shaping the future of non-destructive testing.
About Our Guests: Lennart Schulenburg is a prominent figure in the field of industrial X-ray technology, currently serving as a key executive at VisiConsult, a family-owned company renowned for its innovative X-ray systems and solutions. With a rich background in developing high-energy X-ray systems, Lennart brings a wealth of knowledge and experience to the podcast. His expertise extends to improving industrial X-ray safety and adapting technology for non-medical uses, making him a vital resource for understanding the intricacies and advancements in X-ray applications.
Topics Covered: Throughout the episode, we cover a wide array of topics centered around the utilization of X-rays in industrial settings. Discussions include the differences between medical and industrial X-ray technology, with a focus on the energy levels used and the types of materials inspected. Lennart Schulenburg elaborates on the specific applications of X-rays in testing metal parts and electronics for integrity without destruction. The conversation also touches on the crucial aspect of industrial X-ray safety, emphasizing the advanced techniques and safety standards that VisiConsult adheres to in order to ensure the protection of both the operators and the environment.
Our Guest: Lennart Schulenburg- Leading the Charge in X-ray Safety
Lennart Schulenburg is a key executive at VisiConsult, a company known for its pioneering work in the field of industrial X-ray technology. Located in Germany, VisiConsult was founded by Schulenburg’s father in 1996, originating as a small venture that has since grown into an international business. Lennart’s involvement in the company reflects a deep-seated passion for innovation in non-destructive testing, a sector where X-ray technology is used to inspect the integrity of various non-living materials without causing damage. His educational background in engineering, combined with extensive practical experience in X-ray technology, positions him as an expert in industrial X-ray safety, overseeing the development and implementation of complex systems designed to meet stringent safety standards.
Schulenburg’s role at VisiConsult includes leading the design and execution of safety protocols for high-energy X-ray systems used in industrial applications. These systems are critical in sectors like aerospace, automotive, and electronics manufacturing, where they help ensure the quality and safety of components that must meet exacting standards. Under his guidance, the company has developed X-ray solutions that significantly enhance industrial X-ray safety, incorporating cutting-edge technology and automation to reduce human exposure to high-energy radiation. His work emphasizes the importance of maintaining rigorous safety standards, not only to comply with global regulations but to advance the technology’s application safely and effectively.
Beyond his technical contributions, Lennart Schulenburg is actively involved in fostering innovation within the broader industry. He frequently speaks at conferences and participates in panel discussions focused on the future of non-destructive testing and the integration of artificial intelligence into industrial processes. His insights into how AI can improve defect detection and operational efficiency highlight his forward-thinking approach to industrial X-ray safety. Schulenburg is not only a figure of authority in the X-ray technology sector but also a visionary who sees beyond the immediate technical challenges to the potential transformations in industrial practices through advanced technologies. His leadership at VisiConsult has been pivotal in steering the company toward new frontiers in industrial safety and efficiency, making it a leader in its field globally.
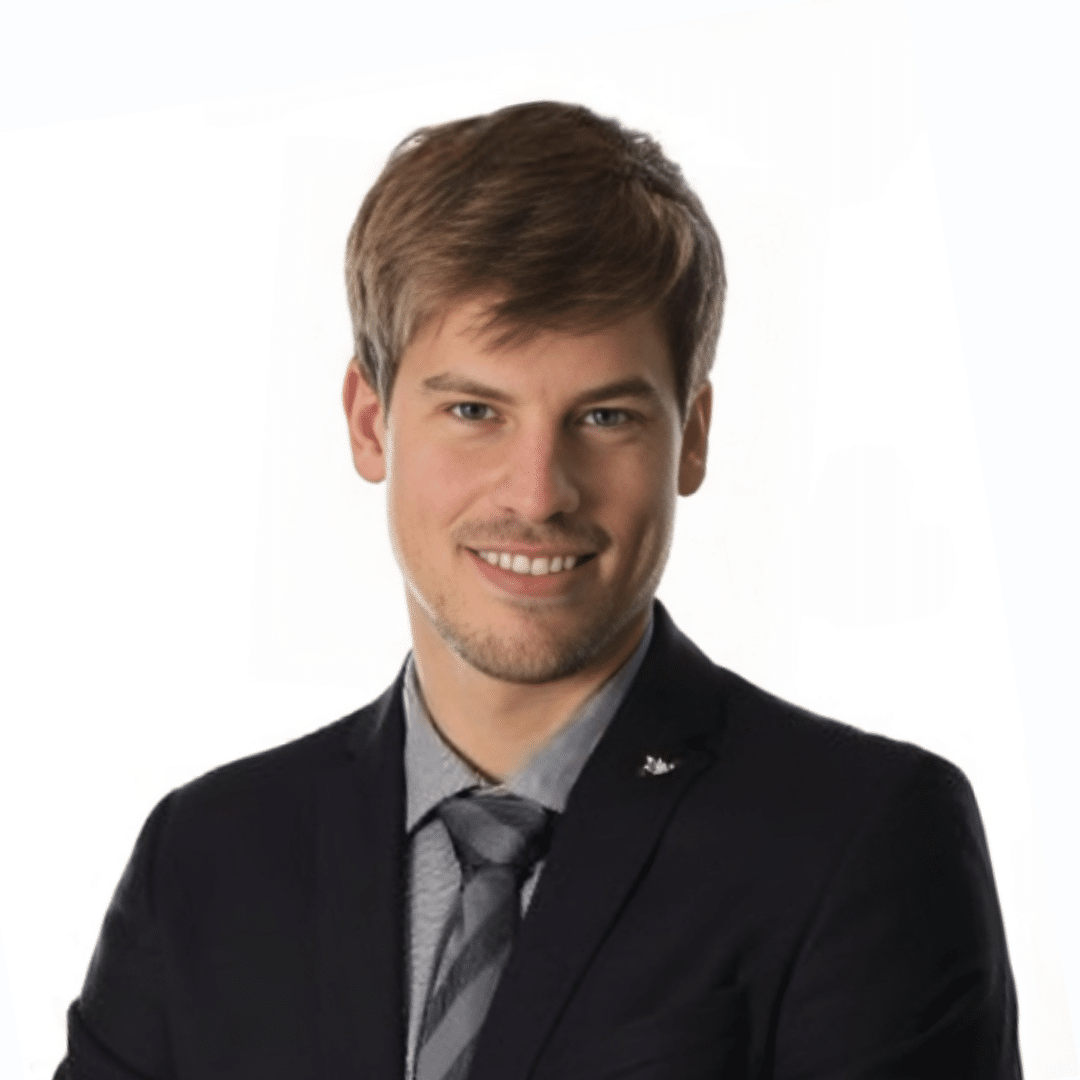
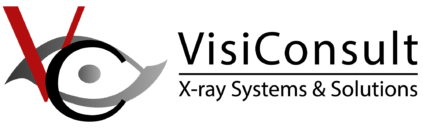
Episode Transcript
Lennart Schulenburg: If you’re sitting on an electric vehicle, you sit on a bomb, effectively because there’s a lot of chemistry just beneath you that has a lot of energy packaged up inside. If that thing malfunctions, it melts this car to just a clump of metal because it gets incredibly hot. These things are incredible to take out. Firefighters have a lot of pain with dealing with these new EVs. So what, Of course, all these manufacturers are trying to ensure that they are functioning correctly and that there is no maybe a short circuit that results in a fire. How can that be ensured only by non-destructive testing? Because what you cannot do is open every battery and look whether it’s broken. Because once you’ve done that, the part is broken. So people do that and sample from the line and maybe cut open every 100th part. That’s not a sustainable measure. So this is where our equipment comes in and really literally looks at every battery, every casting, every electronics part that’s coming off a manufacturing line, and then uses image processing to make sure that there are no defects on the inside.
Jennifer Callahan: Welcome to the Skeleton Crew. I’m your host, Jen Callahan, a technologist with ten-plus years of experience. In each episode, we will explore the fast-paced, ever-changing suburbs, and the completely crazy field of radiology. We will speak to technologists from all different modalities about their careers and education, the educators and leaders who are shaping the field today, and the business executives whose innovations are paving the future of radiology. This episode is brought to you by xraytechnicianschools.com. If you’re considering a career in X-ray, visit xraytechnicianschools.com to explore schools and to get honest information on career paths, salaries, and degree options. Hey, everybody, welcome back to another episode of The Skeleton-Crew. I’m your host, Jen Callahan, and today I have a great guest with me. His name is Lennart Schulenburg. He is joining me from Germany, and he’s here to talk to us today about a different field in which X-rays are being used. So generally we’re talking about health care and the field of radiology. But he’s going to be talking to us about his company VisiConsult. That’s an X-ray system and solutions company. Lennart, thank you so much for being with me today.
Lennart Schulenburg: Thank you for having me.
Jennifer Callahan: My pleasure. I’m excited to delve into what your company actually does because there are a bunch of different sections or segments. I don’t really know the right word to use for it but that VisiConsult has. So I’m going to let Lennart go ahead and explain what the actual company is that they’re using X-ray for, that’s not healthcare-related.
Lennart Schulenburg: Perfect start at the core. We are x-raying everything or let’s put it this way, our customers are x-raying with our systems everything that is not living. So we are not actively active in the medical space. We don’t X-ray humans, we don’t X-ray animals. We X-ray, for example, casting parts, X-ray metallic welds, and these things to check their integrity, whether these things function correctly, whether there are any manufacturing defects inside. This is a field called non-destructive testing because we are effectively doing the same thing as medical health care providers do just that. We’re not checking bones but we are checking metal parts. But we do this in an equally non-destructive way.
Jennifer Callahan: Generally, there are radiopaque and radiolucent materials in X-ray or CAT scan and things like that and X-ray cannot get through metal. Now, is there some variation of X-ray that you’re using that you can get through metal?
Lennart Schulenburg: Excellent question. Because we use the same x-ray as you use in medical but we use much more energy. So a normal system of ours starts at 225 kV. While I know in the medical space you are more likely in the 40 to 60 kV range if you look at tissue and you might correct me whether maybe that is even too high already. But this is where we start. We have systems that go up to the 450-600 kV range, and even going up to the linear accelerator range, where you talk about MeV exposure. There’s another distinct difference. We have all the time in the world when it comes to exposure. You want to limit exposure when it comes to humans, absolutely clear that sometimes we have exposure times that are minutes long, or we have CT scans that take ten hours and we spin the part, by the way, which you would never do with a human being. You spin around the human but we actively don’t have all these constraints. So we take much more energy, we take much longer time, and we can do things with our object of interest that you could never do in the medical.
Jennifer Callahan: Wow, that’s really interesting. For those of you who are listening, who might not know exactly what kV is, it’s the force of the X-ray coming out. Did I explain that right?
Lennart Schulenburg: That is right. So you look at kV and Ma. While kV is like the force of this thing coming out, which just determines the penetration, the Ma, the milliampere would be like how many photons would come at a time. We use tubes that have around 1000W sometimes. So it’s a lot of photons coming. You would never expose a human to that dose but if you have a metal object, you don’t care.
Jennifer Callahan: As you were saying, you are actually kind of low at the end of the kilovolts that we use. So for an extremity, you’re usually using somewhere around 50 kV. Then once you get into thicker body parts you’re using a higher kV. So your highest kV is, I’d say usually like 125. That’s where a chest X-ray is about between 70 and 80 for your thicker extremities or your abdomen. But the highest is 125. So for those of you who are listening, it gives you an idea of how much higher you’re starting at the 200th and you’re going up and you said into the linear accelerator. So that’s being used for radiation therapy, right?
Lennart Schulenburg: Exactly. So if you, as a human, accidentally become trapped in one of our industrial inspection systems for longer than a minute, your body would start dying effectively, which is why there are a lot of safety measures in place. There are lead-lined cabinets around it and a lot of safety protocols on the inside. So actually that should and does never happen. But it puts these things in perspective. Those at this rate are deadly. You have to do measures to put in place measures that are protecting human lives.
Jennifer Callahan: Would you almost kind of equate that to different nuclear destructions that have happened, like Chernobyl, almost like how the people were exposed to so much radiation in such a short amount that led to actively dying?
Lennart Schulenburg: Exactly, that amount of dose where these things actually get very detrimental to your health in the long run but potentially also in the short run, if you just catch enough dose. But this is actually why there are companies like us who know how to handle X-rays. We know how to put the safety measures in place. There are, of course, a lot of certifications around it, like the FDA in the US is a big governing force that makes sure X-ray systems being put in circulation, are safe to use in an industrial sense.
Jennifer Callahan: Now, for the people who are operating equipment that are doing the testing, what does their background look like?
Lennart Schulenburg: That’s interesting because it’s a little bit different than in the medical field, most likely people from material sciences. So these are people that are looking at the metallurgists, that are looking at the integrity of parts. There is no real profession, X-ray tech, I mean, there is a profession called non-destructive testing and X-ray inspection is one subfield next to ultrasonic inspection. You’d be surprised there are many more medical technologies that are applied to materials too. So there is kind of like a trait that you can learn but there is no general field of activity, like doctors and X-ray techs and all these things. It’s mainly people coming from the world of quality and material science.
Jennifer Callahan: Your company’s been around for some time and it was started by a family, and it’s still pretty much family-run and within the family.
Lennart Schulenburg: Yes, that is the case. We were founded in 1996 by my father. We started as a one-man shop. My mother was our second employee. We grew slowly over time. We were none of those supercharged startups you see these days. We grew completely organically with no investors, slowly, steadily, and conservatively. We grew into 250 people, which we just hit last year, where global business, 80% export quota and our customers are the likes of Blue Origin, Space-x, Boeing, Pratt and Whitney, and BMW. So names that every of us is aware of and knows about, we focused on the high-tech equipment side to enable these cutting-edge technologies like additive manufacturing, 3D printing, and space travel.
Jennifer Callahan: Wow. Where was the vision for your dad to start up a company like this? It’s not really something that you kind of like to pick out of the air. I feel like some people who go into entrepreneurship like they’re opening up a restaurant or something along those lines. But your dad started up an X-ray company.
Lennart Schulenburg: See, he was working as the head of development for one of the oldest X-ray businesses in Germany. They started to work with Mr. Roentgen, the founder of the X-rays. This company was bought by GE, General Electric back in the days. What he did not want to be part of a multi-billion global conglomerate that was more like a faceless entity. So he really wanted to have purpose and work on something that drove him forward and energized him. So he quit. That’s when he started to like, found VisiConsult as a spin-off from GE, you could say. So there was no broader plan. It was more like a necessity that this was the thing that he did not want to do. He saw the chance in building something on his own to do things differently.
Jennifer Callahan: It’s truly admirable of your dad that he followed his vision and opened up his own company. I admire that. Growing from a small company and as you said, 250 employees and different projects that are there. So you guys are doing I was on your website earlier and you just did name a few. You do VC battery, VC count, and then the VC security was the one that caught my interest when reading about it. Could you give a little explanation of those three different categories?
Lennart Schulenburg: Yeah, we have our main business line which is the non-destructive testing line. But then there is the VC count, is our electronics label the VC battery, a pretty interesting one, it is doing very fast CT scans of batteries. So if you look into a Gigafactory of Tesla, for example, these things churn out batteries in between 1 to 2 seconds per battery. This is the pace at which these batteries are getting produced. So you need ultra-fast inspection equipment. What we’ve developed is a computer tomography scanner that scans a battery a second. So you can imagine how fast this thing has to be to really do that at high resolution. Our VC security line is our public security business, which produces mobile bomb diffusion or bomb detection equipment. You are aware of the systems at the airport that the TSA operates, these are the stationary systems. But if somebody just put a backpack somewhere and nobody knows what’s inside, then the response units come there but one of our portable X-ray units and kind of look inside the baggage and make sure that there is no bomb or IED or other things inside.
Jennifer Callahan: Wow, that’s pretty amazing. I’m assuming something like that is utilized through multiple different countries, maybe not just only in airports but in bomb units. I feel like, unfortunately, in this day and age, there’s always either one mass shooting or bombings of some sort. That would be some pretty great equipment to have on hand, that’s awesome.
Lennart Schulenburg: Especially, in the Middle East, there’s a lot of demand for these things, unfortunately, right now. You look a couple of miles to the east, you look at Ukraine, there are a lot of needs to deal with all this leftover ammunition and this is where these systems are used. It gives our employees a great sense of purpose to play a part in making the world truly a little bit safer through that technology.
Jennifer Callahan: You’re talking about, just to go backward, the non-destructive testing. So I guess to scan something or you’re saying non-destructive is obviously you’re not taking anything apart, you’re testing or like for the batteries to be able to scan those, they don’t have to get broken down and the integrity is held. Do a little bit more explaining that, because I feel like I just mismash through that.
Lennart Schulenburg: No, you got to the point. These batteries, I mean, effectively, if you’re sitting on an electric vehicle, you sit on a bomb, effectively because there’s a lot of chemistry just beneath you that has a lot of energy packaged up inside. If that thing malfunctions, it melts this car to just a clump of metal because it gets incredibly hot. These things are incredible to take out. Firefighters have a lot of pain with dealing with these new EVs. So what, Of course, all these manufacturers are trying to ensure that they are functioning correctly and that there is no maybe a short circuit that results in a fire. How can that be ensured only by non-destructive testing? Because what you cannot do is open every battery and look whether it’s broken. Because once you’ve done that, the part is broken. So people do that and sample from the line and maybe cut open every 100th part. That’s not a sustainable measure. So this is where our equipment comes in and really literally looks at every battery, every casting, every electronics part that’s coming off a manufacturing line, and then uses image processing to make sure that there are no defects on the inside.
Jennifer Callahan: You go then to the manufacturing site and this equipment is installed there.
Lennart Schulenburg: Exactly, our company is providing the equipment that’s been used by our customers in their production plant. We also offer something we call inspection services. This could be much more compared to, let’s say, a radiologist who has a CT machine. So people come to us with their parts and we give them a verdict of whether it’s good or bad but that doesn’t scale. If you have an R&D department and you have three parts, you can bring it somewhere and get it scanned and not buy a complete CT scanner. But if you are a production facility like Tesla, you need to have your own equipment.
Jennifer Callahan: This episode is brought to you by xraytech.org, the Rad Tech Career Resource. If you’re considering a career in radiology, check out xraytech.org to get honest information on schools, degree options, career paths, and salaries. When you’re talking about X-raying the cast, is that making sure that there aren’t cracks in it?
Lennart Schulenburg: Exactly, yes. Especially, the safety-critical ones are more important. Let’s imagine the part where your wheel is attached to your car. It’s called the wheel suspension. So this is a cast part out of aluminum casting because we want to be sustainable these days. So we use aluminum and not steel. But the challenge with aluminum, you have incredibly thin structures because you want to be as weight-effective as possible. So just a tiny crack or a tiny porosity could make the part fail. On the outside, looks great, but if you go maybe to Germany on the autobahn, you can do that, You go, I don’t know, 150 miles an hour, You can do it, you shouldn’t but you can. Then it breaks because this is when the forces are applied. So we look inside, we see the porosity and then this part can be rejected.
Jennifer Callahan: It’s interesting. As you said, it’s truly put to the test. So if there was a crack in it, it would be at that high. I think, in the United States, our speed limit is maybe 80. They don’t want you traveling any faster. Not to say that some people do not.
Lennart Schulenburg: It’s not advisable. Just because you can, you shouldn’t.
Jennifer Callahan: Right, I agree with you there. So you guys have a lot of great stuff going on. Have you met any challenges along the way in trying to develop these new processes?
Lennart Schulenburg: Yes, a lot. For companies to implement, there are challenges starting with the price. You know, X-ray machines are nothing cheap in the medical world, that’s the case. But in the industrial world, it’s even much bigger because we have less scale than the medical industry. The human is an incredibly from an engineering standpoint and incredibly standardized part to look at. If you want to put it like this, we all kind of like are roughly the same size, we have a head, mostly, we have a lung, and we have two legs mostly but it’s something you can standardize around. If you want to standardize in the industrial world, it’s much harder because you can look at an aircraft wing one day and you can look at an additively manufactured turbine blade the next day. You could look at an aluminum part or a honeycomb carbon fiber part, and the next day you look at an Inconel superalloy that is highly X-ray absorbent. So the variance is incredibly high. This increases, obviously, the cost for people implementing that. But then there’s everything that’s around regulation. So you need to have people that are trained in operating X-ray equipment. You need to have the regulatory approvals to actually be able to put them to work. You need to supervise them, you maintain them.
Lennart Schulenburg: There’s a lot of challenges for our customers. Obviously, we, as a solution provider, face the same issues in a highly regulated environment where you need FDA approvals and FDA accession numbers and all these interesting things that you need. Even then, just putting the physical tool in place is just one part of the story because you need to do something with the data. That kind of like brings us to where we focus a lot now, the AI driven automated image processing algorithms that actually find these little defects. This is where the tie back to the medical world is. You are also looking kind of for defects, I would say. I mean, if you look for a tumor then you could say is a defect. That’s something that shouldn’t be there as an anomaly. It’s very similar in the industrial world. That porosity is a defect. It’s a tumor in the part that shouldn’t be there. This is where we invest a lot of our time and effort into these AI algorithms to automatically find them because finding skilled X-ray techs is incredibly hard these days, especially if you’re in a factory in Nevada working three shifts, seven days a week, that’s not something many people want to do.
Jennifer Callahan: That brings me to you guys have expanded from Germany and now you’re in other parts of the world.
Lennart Schulenburg: Yes. Well, our humble beginnings are in Germany, north of Germany, to be precise, close to Hamburg. Our first subsidiary that we opened abroad was in Atlanta, in the US. So the US is one of our most important markets as a very industrialized country with a lot of need for high-end machinery and equipment. But we are also active in Brazil, China, and India, so truly global.
Jennifer Callahan: Do you have different manufacturing sites in all of those areas?
Lennart Schulenburg: Yes. we, partially, have manufacturing sites, even though the core comes out of our factory in Germany, and then we just build the enclosure and the surrounding. So it’s not sustainable and not sensible to transport a 30-ton lab room around the world if you can produce them locally. So we try to be smart about what to localize, what to do in the local economies, and what to do from a central technology hub.
Jennifer Callahan: Challenges that you face but obviously you guys are doing something right, that you keep growing in different countries and you have these different areas that you do your X-ray on. Do you guys set goals yearly? You have the VC security, how long did that take for that to come to light, or even for the VC battery, how long does it take for an idea to come to fruition I guess I’m asking?
Lennart Schulenburg: Yes, the VC battery is a good one because we’ve just found it last year. So the seed was planted the year before the last year. So we got contracted or contacted by a big automotive OEM that needed a solution, and we had an idea and scaled that up very quickly into a business on its own. This year alone, we are looking at an order intake of 15 to 20 million just coming from that division alone. So we are scaling quite quickly, just by the way we are set up in an agile mindset, having the startup mentality still within us. This is what makes us so successful. It’s funny that you mentioned quarterly goals because we manage the company by what is called OKRs. So objective key results, which is a very cool technique to manage performance because you’re not setting out these long-term yearly targets and then measuring milestones along the way but you’re casually meeting with the people you work with once a quarter and everybody sets their own targets for the next quarter, which is then called an OKR. So it’s nothing that’s mandated top-down but it’s a bottom-up approach where everybody says, I want to achieve these three things, and we write them on the wall and we note them down. That’s how we drive things forward. Obviously, we check that they are in line with the broader vision and the broader goal but they are self-set, intrinsic targets coming from the people.
Jennifer Callahan: Different ideas coming from different people that come forth, not necessarily that say like yourself or your dad came up with one of the new processes that your guys are doing that might have came within the company that and everyone worked towards doing it.
Lennart Schulenburg: Absolutely, not. We focus a lot on a lot of empowerment of the people. We try to hire the smartest people we can attract and it would be very arrogant to tell them what to do. Obviously, we need to run in the right direction but we try to manage the company more like a fleet of speedboats and not like a big tanker. This fleet of speedboats brings success and sometimes endeavors fail. This is part of the journey. Not everything works but maybe 70% works. Those 30%, this is just part of the process. This happens and in our corporate culture, these people, they’re not ashamed of their failures. But this is, we need to fail in order to win.
Jennifer Callahan: Not to say that your failure now wouldn’t be a success later. Sometimes, you just haven’t figured it all out on how to make something work.
Lennart Schulenburg: You’re absolutely right. There’s a famous example in this that doesn’t come from our industry but it’s the 3M sticky note. So that was considered a failure for years because it didn’t stick. 3M was in the business of developing tape that sticks. You needed to find a purpose for this thing that was being built. So we have that many times that there’s an innovation or an idea or something that’s been built that just doesn’t fit. We shelve it and maybe it’s dead forever, or we pull it out and use it for a different application. But this requires creativity and openness of mind.
Jennifer Callahan: Where are you guys looking for the future? I mean, do you guys have a plethora of ideas that you’re working on, or are you looking at what you currently have and honing that even more? Where are you guys moving towards in the future?
Lennart Schulenburg: There’s one big dimension on which we focus on and that’s software and artificial intelligence. We started roughly six years ago to completely focus nearly all of our development efforts, development funds, and activities on these fields, and we have achieved quite a breakthrough there. For example, our compass, our AI-powered automatic image processing tool, has a detection rate, the true positive rate for Porosities, for example, of 98%, which is by far exceeding the detection capabilities of a human. I think you can see similar things in the medical world where I think AI is exceeding the detection rate of human doctors or radiologists in many with a much higher consistency and a much faster pace. So the whole digital world is where we focus most of our attention these days.
Jennifer Callahan: AI is just blowing up everywhere but it’s great. I mean, in the medical world, they’re using it as an aid for the radiologist. It’s not taking the place of the radiologist and the radiologist, different companies that I’ve spoken to on the podcast about the AI technology that’s out there that is being used, as I said, have the ability to go with what’s being suggested by the technology or to not include it. Say, if you know they’re looking at a node on a lung image, do they think it’s suspicious? It’s being highlighted by this technology, they can put in there for you to follow up or even other AI technology, helping radiologists produce the readings just to make their workflow go a little bit faster but at the end of the report, they have to okay it basically like they don’t have to go with what the report is generated by. But it’s great that the digital world is exploding. I feel like it’s come such a long way from the early 90s, dial-up days to now we have, computers doing lots of stuff.
Lennart Schulenburg: It’s the same in our industry, by the way. Currently, we are talking about assistance features that these AIS are providing. But let’s fast forward a little bit and let’s look into the future. If you would ask me, I would say that will not last forever. If I look at the rate at which AI is improving and getting better, and the rate at which humans are improving due to our nature where we are over millions of years. I think humans cannot keep up with the diagnostic tasks that have been put to us. AI will, my strong belief, it’s my honest, humble opinion. I’m not saying this will be the case but AI will be better than humans at certain diagnostic tests in the absolute near future. This does not mean that humans are not necessary anymore. But this means we humans can focus a lot more on what we humans are good at. Maybe now I’m making a comment toward the healthcare world. I think what we don’t have enough time for is interacting with people, interacting with patients, delivering maybe tough messages, and doing the empathic world. I think that will be something that humans will have to do a lot more, both in the industrial world but also in the medical world, interpreting AI results and delivering them to humans and being there for the human interaction because this is what we are truly good as living beings while the AI is super good at detecting anomalies in large amounts of data.
Jennifer Callahan: That’s a good way to look at it. So, I mean, not to be on a whole spiel about the AI but, as you said, it’s there to help humans but ultimately humans are the ones that are developing it. So it’s doing what we’re telling it. It’s not like the computers are all crazy on their own. But it’s so interesting how you don’t realize that AI is integrated into so many different parts of your life, systems, and stuff. So moving with the digitalization, with your company and everything that you guys have going on, I mean, you’ve got so much you guys have to be truly proud of where the company has started and where you currently are now.
Lennart Schulenburg: Absolutely. It’s something to be proud of but I think there’s just so much more we can do and so much more that is being worked on. It’s definitely an exciting time to work on these technologies because there are so many breakthroughs left and right with cloud, connectivity, AI, and robotics. It’s a fun time.
Jennifer Callahan: For sure. So, everybody, this is Lennart Schulenburg with me today talking about a different realm of X-ray, probably definitely scanning things that are within your household or as you said, your cars or your batteries. So really interesting conversation. Thank you so much for sharing your wealth of knowledge and what you guys do there.
Lennart Schulenburg: Thank you, it was a pleasure.
Jennifer Callahan: Great. All right, everybody, my name is Jen Callahan. I have Lennart with me. We’re going to say goodbye for the day. But check in with us next week for another great topic that we’ll be going over. Thanks, guys. You’ve been listening to the Skeleton-Crew, brought to you by xrayTech.org, the Rad Tech Career Resource. Join us on the next episode to explore the present and the future of the Rad Tech career and the field of radiology.